Unterabschnitte von Startseite
Schnupperlehre
Die weltbesten Anlagen für Spraydosen
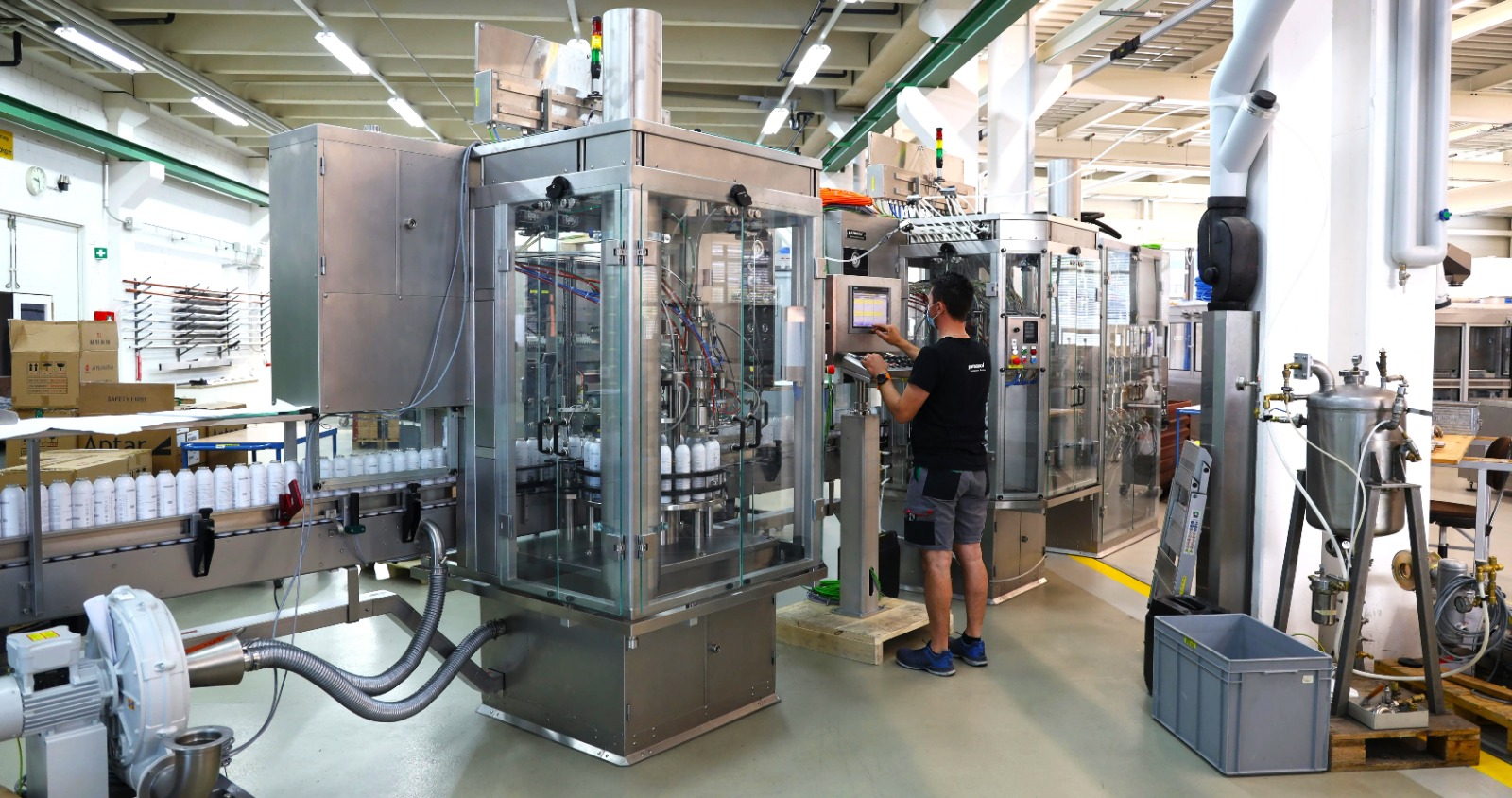
Interessiert dich der Beruf des Automatikers? Dann nichts wie los, melde dich zur Schnupperlehre an und du erhältst einen Einblick in die spannende Welt des Maschinenbaus – angefangen von der mechanischen Bearbeitung und Montage, über die Verdrahtung von Elektrokomponenten bis hin zur Pneumatiksteuerung und Softwareentwicklung.
Im obigen Bild testet ein Pamasol-Mitarbeiter einen Macromat LB20. Das ist eine Abfüll- und Verschliessmaschine für Spraydosen. Während sich Polymechaniker und Metallbauer um Mechanik und Metallteile kümmern, baut der Automatiker alle elektrischen Komponenten wie Sensoren, Motoren und den grossen Touchscreen an. Im Anschluss wird die SPS (das ist der Computer und somit das Hirn der Anlage) programmiert und damit der Maschine Leben eingehaucht.
Sobald die Anlage funktioniert und vom Kunden abgenommen wurde, wird sie in an den Produktionsstandort versendet. Das kann beispielsweise Australien, die USA oder Brasilien sein, aber auch Deutschland und die Schweiz. Es gibt Pamasolanlagen auf der ganzen Welt, welche Milliarden von Spraydosen produzieren.
Ausgelernte Automatiker haben die Möglichkeit, andere Länder und Kulturen kennenzulernen. Denn die Anlagen, welche über die ganze Welt verteilt sind, werden durch Pamasol-Mitarbeiter vor Ort in Betrieb genommen und gewartet.
Aufgefallen ist es dir wahrscheinlich nicht, aber du hattest bestimmt schon eine Spraydose in der Hand, welche auf einer Pamasol Anlage gefüllt wurde (Deo, Farbspray, Backofenreiniger, Rasierschaum, WC-Duftspray, Silikonspray, Öl-Spray, …die Liste wäre noch viel länger).
Folgend einige Antworten zu Fragen, welche uns oft gestellt werden.
Sind Automatiker gefragte Berufsleute?
Ja, Automatiker sind sehr begehrte Berufsleute und sie werden es auch in Zukunft sein.
Immer mehr Aufgaben und Arbeiten werden von Maschinen und Robotern übernommen. Damit das möglich ist, braucht es Automatiker. Sie bauen diese Maschinen und schreiben die zugehörige Software.
Wie lange dauert die Lehre und wo geht man zur Berufsschule?
Die Lehre dauert 4 Jahre. Während dieser Zeit besuchen die Lernenden an einem bis zwei Tagen pro Woche die Berufsschule in Arth-Goldau. Macht man die Berufsmatura während der Lehre, hat man in allen vier Lehrjahren zwei Tage Schule.
Zusätzlich zur Berufsschule besucht man die überbetrieblichen Kurse im Ausbildungszentrum der Swissmechanic in Pfäffikon SZ. Diese Kurse dauern jeweils einige Wochen.
Welche Weiterbildungsmöglichkeiten gibt es?
Es gibt enorm viele Weiterbildungsmöglichkeiten wie beispielsweise die Berufsprüfung zum Automatikfachmann oder die Höhere Fachprüfung zum Meister Schaltanlagen und Automatik.
Die mit Abstand beliebtesten Weiterbildungen von Pamasol Automatikern waren bisher jedoch die Ausbildungen zum Techniker (HF - Höhere Fachschule) oder das Studium zum Ingenieur (FH - Fachhochschule).
Hat man die Berufsmatura gemacht, kann man sich beispielsweise an der ost.ch in Rapperswil zum Ingenieur weiterbilden.
Was verdient man als gelernter Automatiker?
Pauschal kann man das nicht beantworten. Enorm viele Faktoren wie Arbeitserfahrung, Funktion und Position eines Mitarbeiters oder der Standort und die Branche des Unternehmens spielen eine Rolle.
Was man aber sagen kann: Macht jemand seinen Job gerne und ist Feuer und Flamme für seinen Beruf, wirkt sich das auch positiv aufs Gehalt aus.
Ok, die obigen Angaben helfen nicht wirklich weiter und wir möchten Interessierte nicht im Ungewissen stehen lassen. Folgende Zahlen sind vom Online Portal jobs.ch und können einen ungefähren Anhaltspunkt geben.
Automatiker
- Jobs.ch für Automatiker, abgerufen am 05.06.2022.
- CHF 65'027 Jahreslohn, was bei 12 Monaten einem Lohn von CHF 5'418.90 entspricht pro Monat.
Elektroingenieur
- Jobs.ch für Elektroingenieure, abgerufen am 05.06.2022.
- CHF 96'981 Jahreslohn, was bei 12 Monaten einem Lohn von CHF 8'081.75 entspricht pro Monat.
Video Automatiker EFZ
Wie viele Automatiker hat Pamasol schon ausgebildet?
# | Name | Lehrjahr | Berufsbezeichnung |
---|
50 | Stefan Feier | 2019 - 2023 | Automatiker |
49 | David Bernhard | 2018 - 2022 | Automatiker |
48 | Jonas Bisig | 2018 - 2022 | Automatiker |
47 | Joël Glaus | 2017 - 2021 | Automatiker |
46 | Marvin Büeler | 2016 - 2020 | Automatiker |
45 | Elias Kälin | 2015 - 2019 | Automatiker |
44 | Fabian Suter | 2014 - 2018 | Automatiker |
43 | Sven Faas | 2013 - 2017 | Automatiker |
42 | Lukas Kägi | 2012 - 2016 | Automatiker |
41 | Roman Feusi | 2011 - 2015 | Automatiker |
40 | Tom Lauper | 2010 - 2014 | Automatiker |
39 | Maurus Meier | 2009 - 2013 | Automatiker |
38 | Andreas Kälin | 2008 - 2012 | Automatiker |
37 | Simon Schätti | 2007 - 2011 | Automatiker |
36 | Silvan Donner | 2006 - 2010 | Automatiker |
35 | Urban Bruhin | 2005 - 2009 | Automatiker |
34 | Michel Keller | 2004 - 2008 | Automatiker |
33 | Pascal Kälin | 2003 - 2007 | Automatiker |
32 | Matthias Bamert | 2002 - 2006 | Automatiker |
31 | Roger Kälin | 2002 - 2006 | Automatiker |
30 | Philipp Bruhin | 2001 - 2005 | Automatiker |
29 | André Kälin | 2000 - 2004 | Automatiker |
28 | Yves Gautschi | 1999 - 2003 | Automatiker |
27 | Ernst Späni | 1998 - 2002 | Automatiker |
26 | Patrick Lechner | 1998 - 2002 | Automatiker |
25 | Andreas Schuler | 1997 - 2001 | Elektromechaniker |
24 | Eric Ziegler | 1997 - 2001 | Elektromechaniker |
23 | Ralph Kühn | 1996 - 2000 | Elektromechaniker |
22 | Beat Ziegler | 1996 -2000 | Elektromechaniker |
21 | Reto Inderbitzin | 1995 - 1998 | Elektromechaniker |
20 | Christof von Allmen | 1994 - 1998 | Elektromechaniker |
19 | Patrick Kühne | 1994 - 1998 | Elektromechaniker |
18 | Roman Späni | 1993 - 1997 | Elektromechaniker |
17 | Reto Bachmann | 1992 - 1996 | Elektromechaniker |
16 | Marco Kälin | 1992 - 1996 | Elektromechaniker |
15 | Andreas Knobel | 1992 - 1996 | Elektromechaniker |
14 | Martin Ruoss | 1992 - 1994 | Elektromechaniker |
13 | Marco Räber | 1991 - 1995 | Elektromechaniker |
12 | Kessler Patrick | 1990 - 1994 | Elektromechaniker |
11 | Marco Corvi | 1989 - 1993 | Elektromechaniker |
10 | Michael Kistler | 1989 - 1993 | Elektromechaniker |
9 | Patrik Diethelm | 1988 - 1992 | Elektromechaniker |
8 | Michael Manser | 1988 - 1992 | Elektromechaniker |
7 | Daniel Schätti | 1986 - 1990 | Elektromechaniker |
6 | Oskar Mäder | 1985 - 1989 | Elektromechaniker |
5 | Edgar Pfister | 1985 - 1989 | Elektromechaniker |
4 | Armin Zonder | 1984 - 1988 | Elektromechaniker |
3 | Peter Pedros | 1982 - 1986 | Elektromechaniker |
2 | Josef Schnüriger | 1980 - 1984 | Elektromechaniker |
1 | Reto Hegner | 1978 - 1982 | Elektromechaniker |
Unterabschnitte von Schnupperlehre
Bahnlampe bauen
Das Verschmelzen von Mechanik mit Elektrotechnik
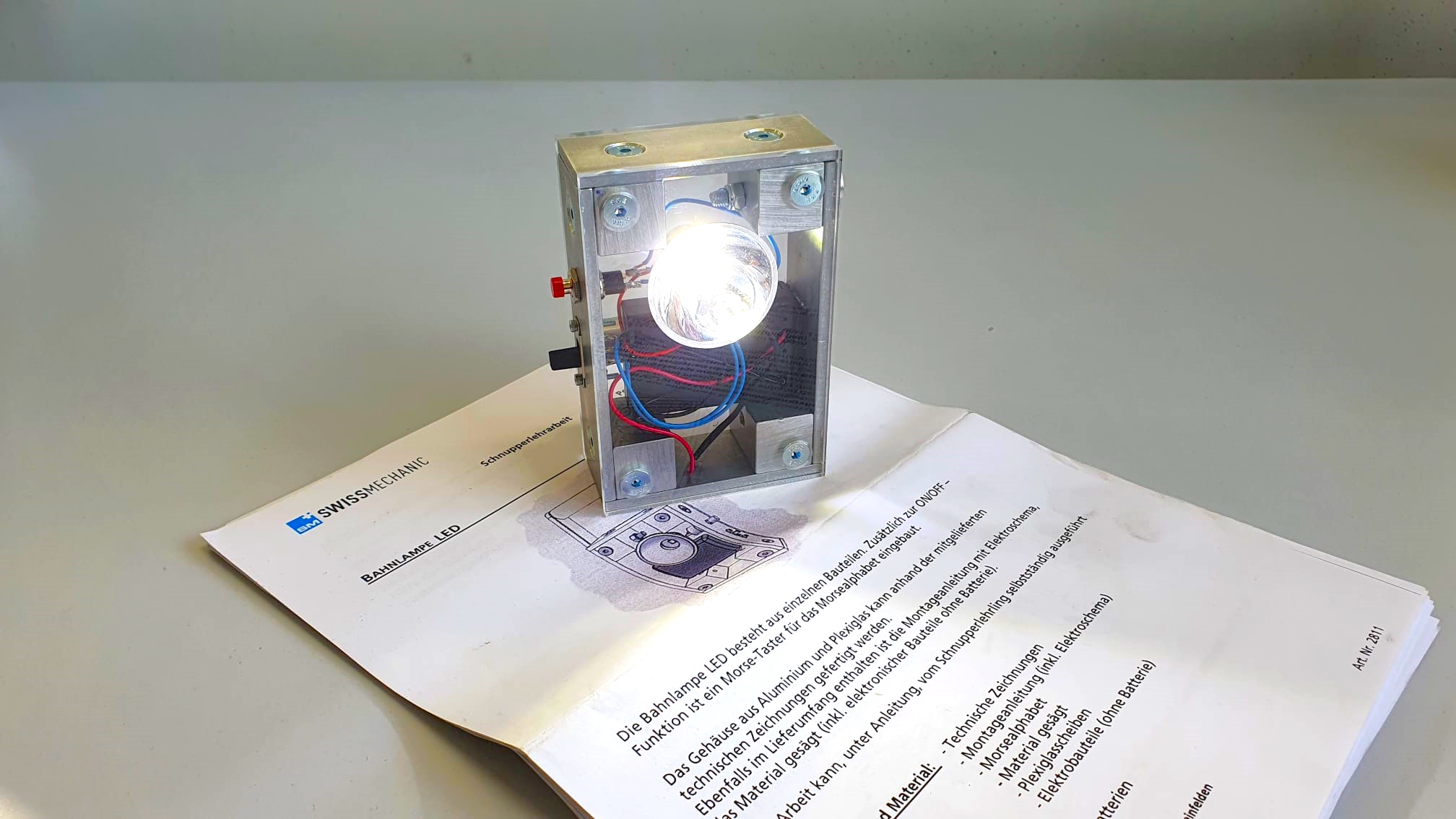
Während deiner Schnupperlehre baust du eine Bahnlampe aus Aluminium- und Plexiglasteilen. Dazu kommen Elektronikteile, welche nach einem Elektroschema gelötet, und somit zu einem elektrischen Schaltkreis zusammengebaut werden.
Bei der Lampe handelt es sich um einen Bausatz, welcher von der Swissmechanic herausgegeben wird. Du kannst die Lampe im Anschluss der Schnupperlehre mit nach Hause nehmen.
Neben der Bahnlampe erhältst du einen authentischen Einblick in unser tägliches Schaffen und die damit verbundenen, spannenden Herausforderungen.
Schaltschrank Steckbrett
Elektroschema zeichnen und verdrahten
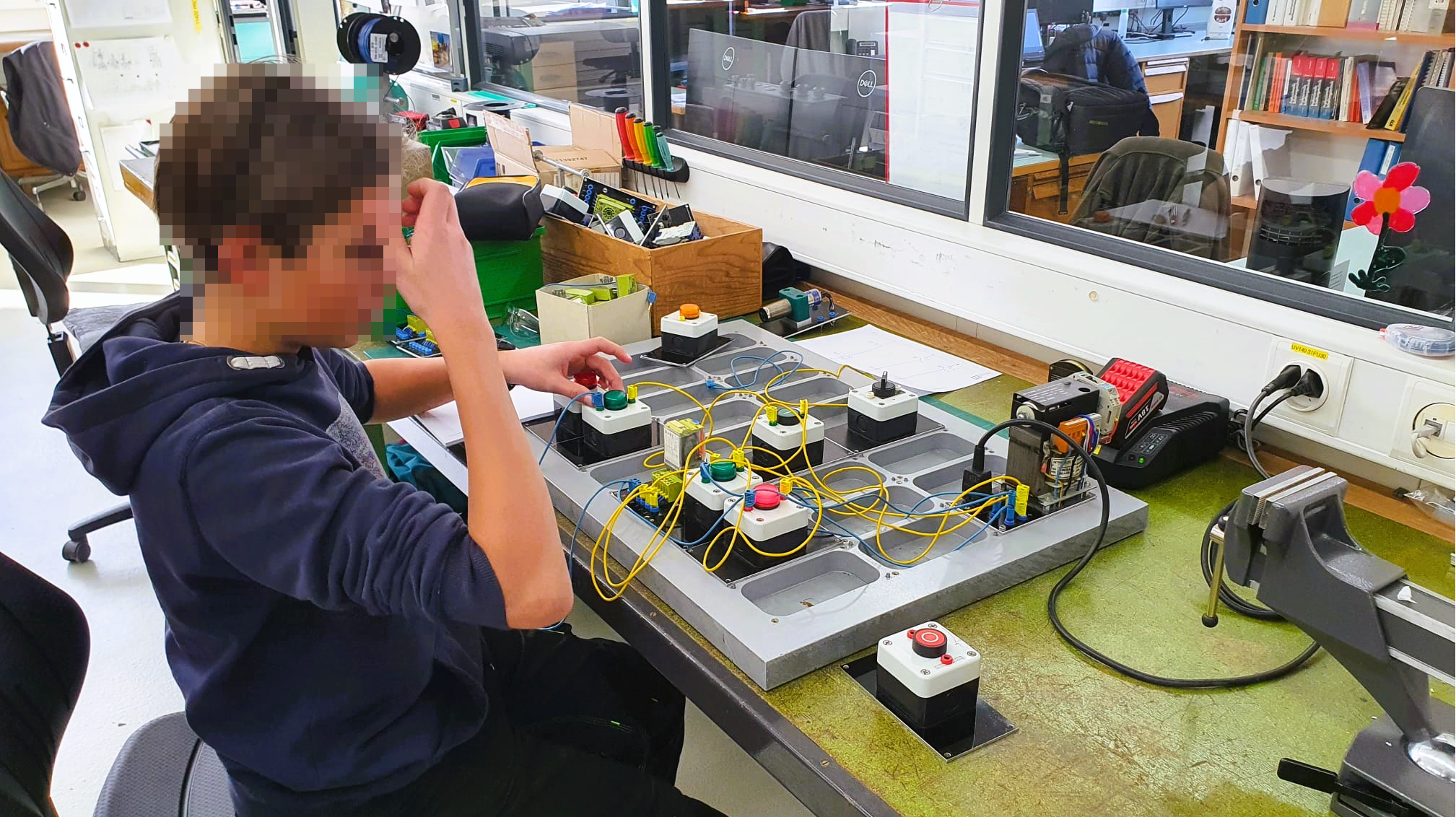
Zu den wichtigsten Aufgaben des Automatikers zählt das Planen und Verdrahten von Steuerschränken. Diese Steuerschränke können mal die Grösse einer Schuhschachtel und mal die Grösse von vier aneinandergereihten, grossen Kleiderschränke haben.
Gefüllt sind die Schränke mit komplexer Elektronik, welche mittels Litzen (flexible Drähte) verbunden werden. Ist von den vielen hundert Litzen nur eine falsch angeschlossen, läuft die Anlage nicht. Im dümmsten Fall gehen sogar Bauteile kaputt, welche so teuer sind wie ein Auto.
Beim Zeichnen des Schemas sowie beim Verdrahten ist somit höchste Konzentration und Vorsicht geboten. Allem voran kommt jedoch das Üben – und genau das wird bei dieser Aufgabe gemacht.
Elektroschema zeichnen via Capital Electra X
Im professionellen Umfeld werden Elektroschemas auf Programmen wie EPLAN P8, Zucken E3 oder WS-CAD gezeichnet.
Für das folgende Projekt empfehlen wir jedoch das einfach zu bedienende CAD Capital Electra X von Radica Software and Siemens. Die Grundfunktionen, welche kostenlos genutzt werden können, sind völlig ausreichend für den gelegentlichen Gebrauch. Zudem muss die Software nicht installiert werden, sie läuft im Internet-Browser.
Normen für das Zeichnen
Wie man ein Elektroschema zeichnet und insbesondere wie die Schaltzeichen aussehen, ist genormt. Das hat den Vorteil, dass die Schemas überall auf der Welt gleich aussehen und dass sie von jeder Elektrofachkraft gelesen werden können.
Die Norm für Schaltzeichen heisst IEC 60617. Die relevanten Zeichen gibt es auf Wikipedia unter folgenden Links:
Keine Angst, man muss diese Zeichen nicht von Beginn weg kennen und beherrschen. Dazu bleibt in der Lehre genügend Zeit.
Aufgaben
Info
Das Elektroschema mit den Aufgaben kann hier als Capital™ Electra™ X Vorlage importiert werden. Wer das Schema nicht online mit Capital™ Electra™ X von Siemens zeichnen möchte, kann es hier als PDF herunterladen.
Alle Aufgaben sind im selben Stil aufgebaut. Links oben gibt es eine Beschreibung mit einem Vorschlag für die zu verwendenden Bauteile. Das 24VDC Potential ist ebenfalls schon eingezeichnet. Oben ist das Plus, unten das Minus.
Zwischen Plus und Minus können die Bauteile eingezeichnet werden. Folgend die Aufgabe 1 als Beispiel.
Vorlage Aufgabe 1

Musterlösung Aufgabe 1

Elektronikprojekt
Roboter programmieren für lernende Automatiker
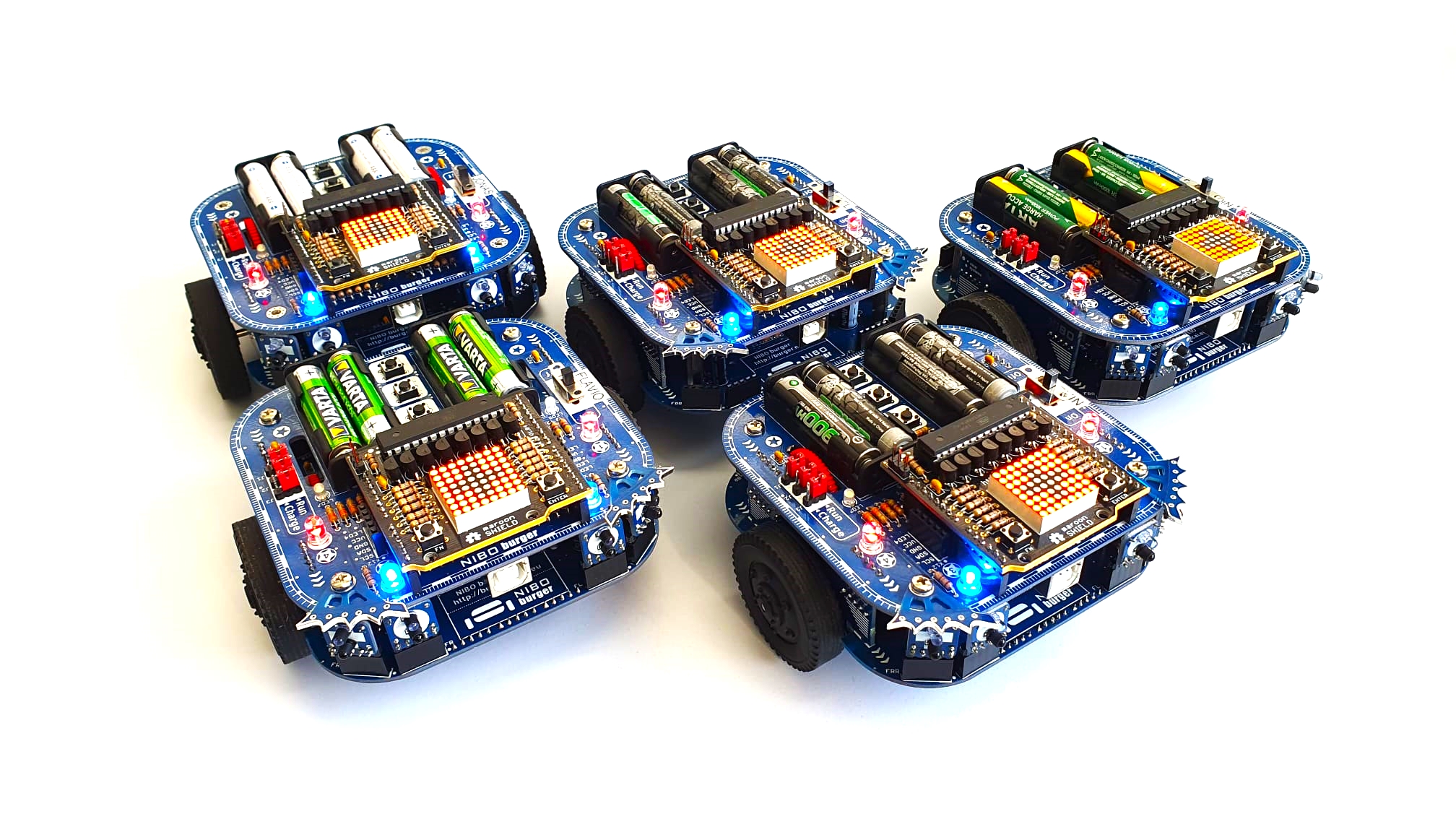
Neben Berufsschule, den überbetrieblichen Swissmechanic Kursen und dem praktischen Arbeiten an Aerosol-Anlagen für Kunden aus der ganzen Welt, arbeiten Automatiker Lernende bei Pamasol auch an Projekten, welche den Fokus auf ein bestimmtes Ausbildungsthema setzen.
NIBO Burger repräsentiert das Elektronikprojekt der Ausbildung. Es handelt sich hierbei um einen kleinen Roboter, welcher von den Lernenden zusammengebaut, gelötet und in der Hochsprache C programmiert wird.
Die Aufgabenstellung, wie auch sämtliche Datenblätter und Wiki Beiträge, sind in Englisch geschrieben. Nach dem Zusammenbau und den Funktionstests, erhalten die Lernenden eine Einführung in die C-Programmierung. Den Projekthöhepunt bilden die unten folgend beschriebenen «Master-Tasks».
Als Bonusaufgabe wird der Roboter mit 3D-Druck Bauteilen optisch aufgepeppt. Folgend als exemplarisches Beispiel ein Heckspoiler.
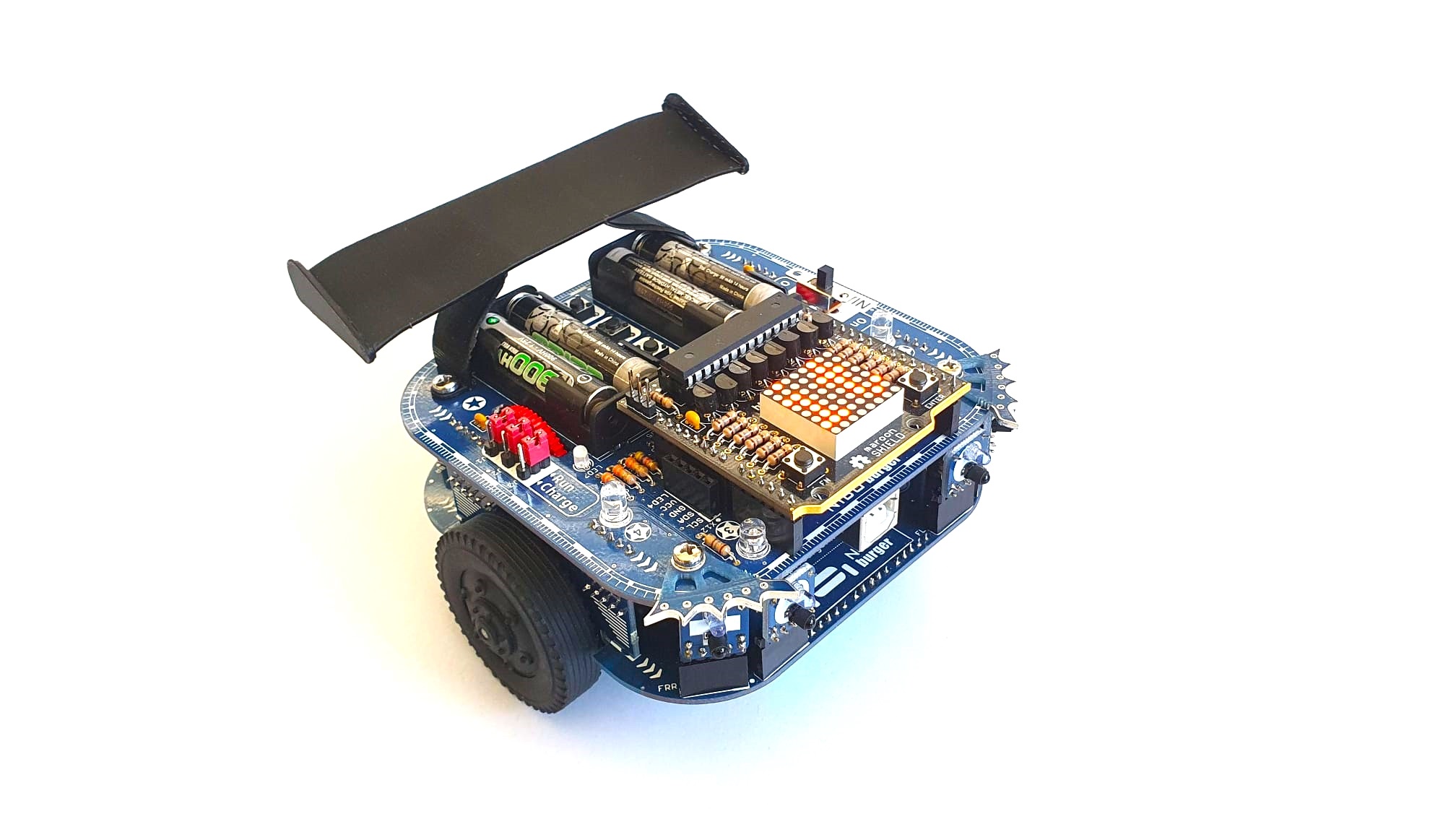
A) Round trip
Der Roboter muss genau 1.5m nach vorne fahren, eine 180° Drehung machen und wieder an seinen Startpunkt zurückkehren. Damit das funktioniert, müssen die Odometrie-Sensoren der Räder ausgelesen und verglichen werden. Basierend darauf werden die PID-geregelten Motoren angesteuert.
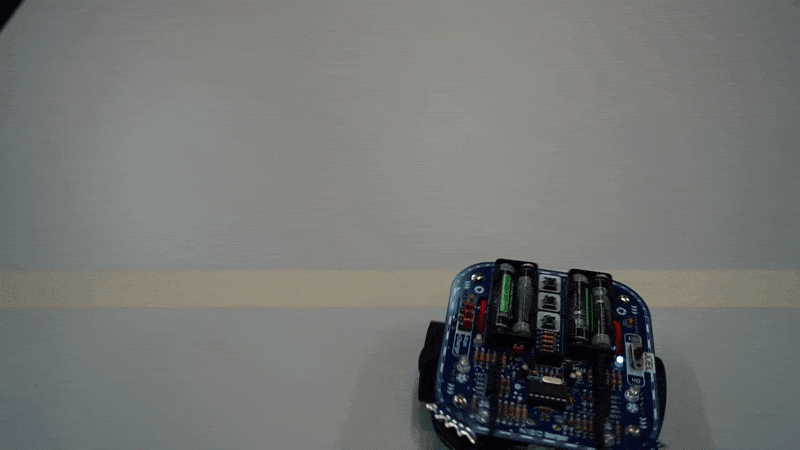
Aufgabenstellung Round trip (Nibo01_V1.0.pdf)
B) Fraidy cat
Frontseitig ist der Roboter mit IR-Bricks versehen. Das sind Infrarotsensoren, welche Hindernisse detektieren können. In dieser Aufgabe geht es darum, den Hindernissen auszuweichen.
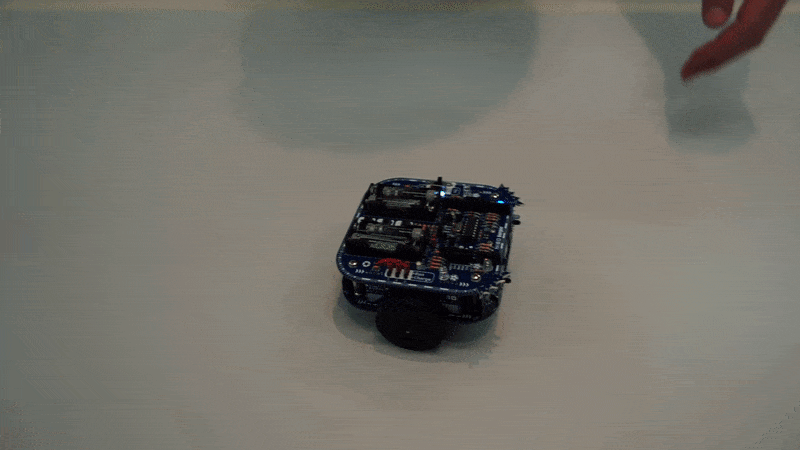
Aufgabenstellung Fraidy cat (Nibo02_V1.0.pdf)
C) Follow me
Im Gegensatz zu Aufgabe B, muss man in Aufgabe C den Hindernissen nicht ausweichen, sondern dem Hindernis folgen. In diesem Fall der menschlichen Hand.
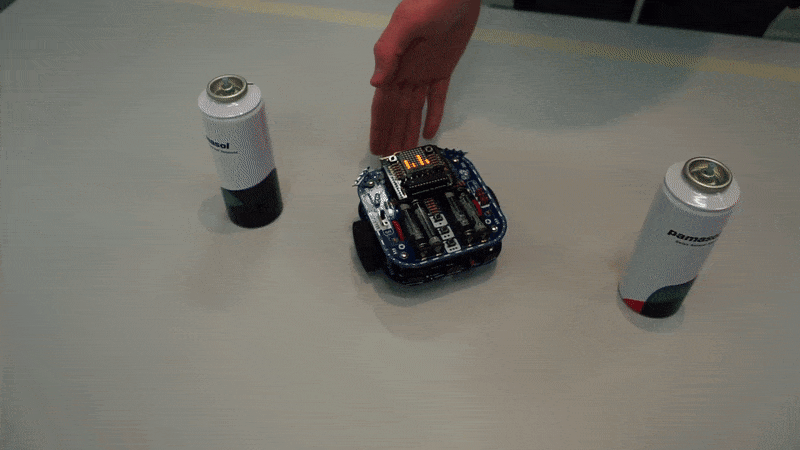
Aufgabenstellung Follow me (Nibo03_V1.0.pdf)
D) Colour detection
Mit den RGB (Rot-Grün-Blau) Farbsensoren müssen die Bodenfarben Schwarz, Weiss, Rot, Gelb, Grün und Blau detektiert sowie auf dem Display angezeigt werden. Das Display läuft eigenständig mit eigenem Microcontroller. Der Microcontroller des Roboters kommuniziert via UART mit dem Microcontroller des Displays.
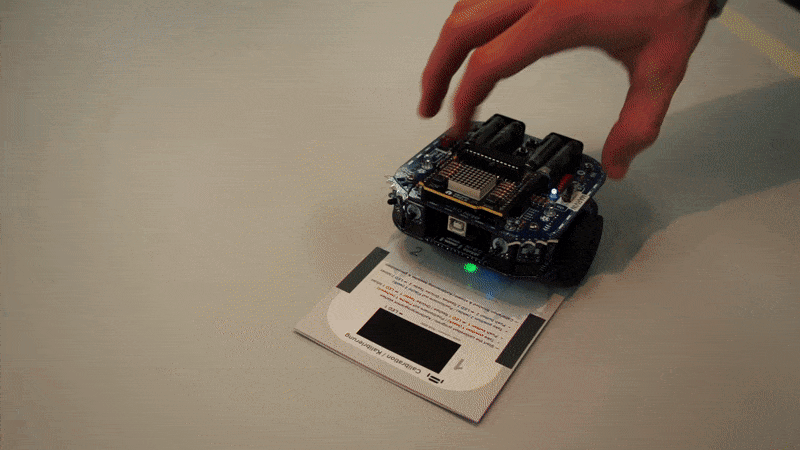
Aufgabenstellung Colour detection (Nibo04_V1.1.pdf)
E) Rabbit warren
In der Königsaufgabe muss der Roboter einer schwarzen Linie auf dem Boden folgen. Die Linie wird mittels Sensoren detektiert und basierend darauf werden die Motoren gesteuert.
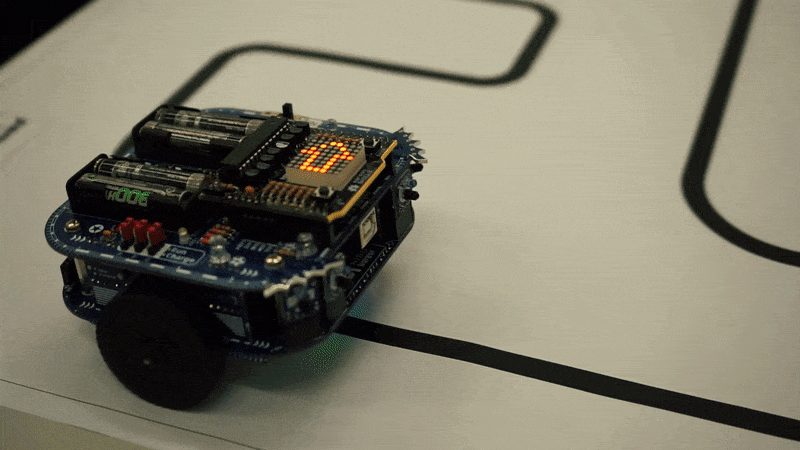
Aufgabenstellung Rabbit warren (Nibo05_V1.0.pdf)
Dokumentation
Die elektrischen Bauteile sowie gelöteten Schaltkreise und die Programmierung werden von den Lernenden in einer schriftlichen Dokumentation zusammengefasst. Folgend können die PDFs heruntergeladen und nachgelesen werden.
Automatisierungsprojekt
Pick&Place Roboter mit Siemens SPS programmieren
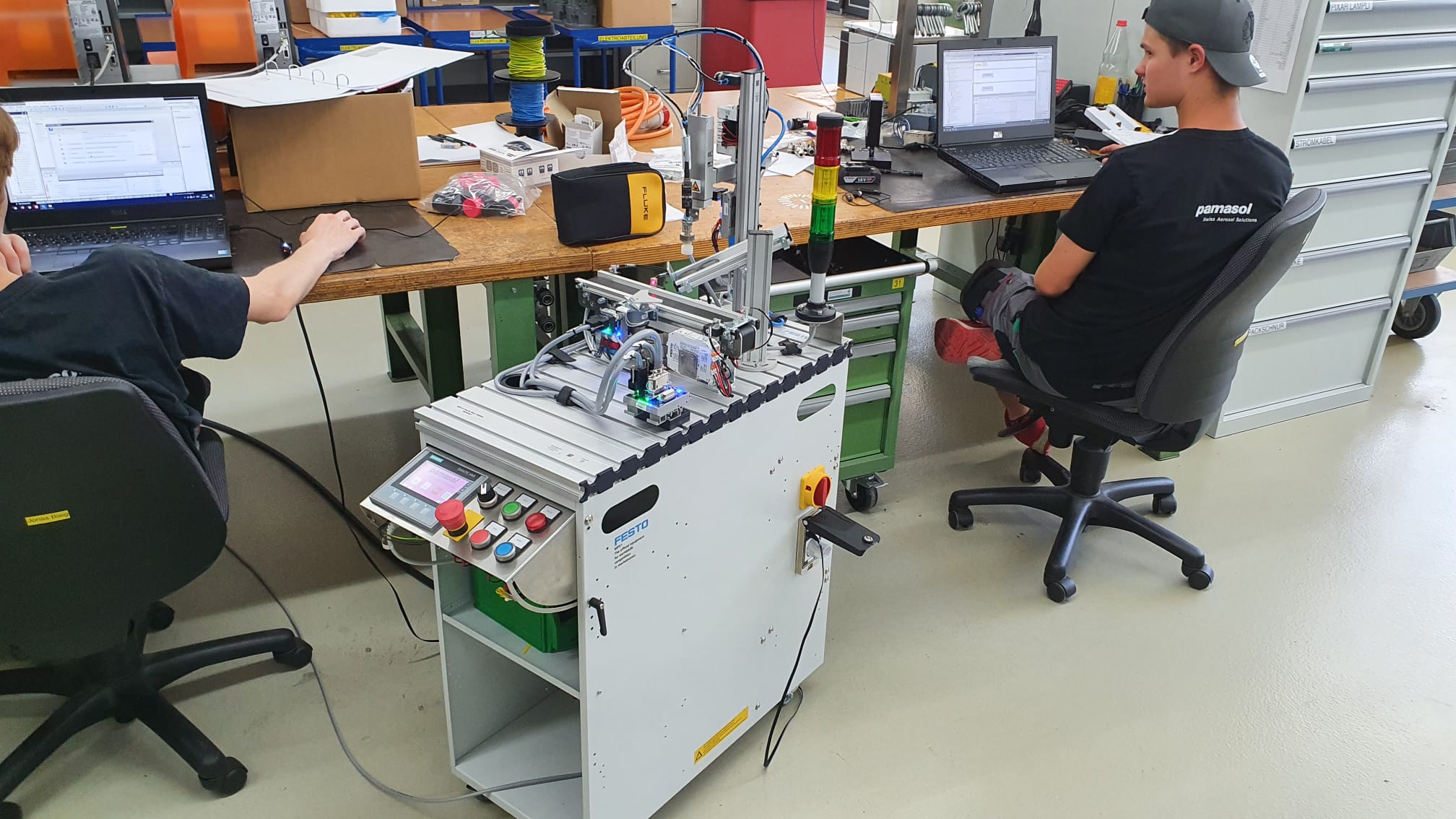
Neben Berufsschule, den überbetrieblichen Swissmechanic Kursen und dem praktischen Arbeiten an Aerosol-Anlagen für Kunden aus der ganzen Welt, arbeiten Automatiker Lernende bei Pamasol auch an Projekten, welche den Fokus auf ein bestimmtes Ausbildungsthema setzen.
Der Pick&Place Roboter repräsentiert das SPS Automatisierungsprojekt der Ausbildung. Es handelt sich hierbei um einen pneumatischen Greifer von Festo Didactic.
Der Roboter wird durch eine Siemens ET200SP SPS (Speicherprogrammierbare Steuerung) gesteuert. Programmiert wird die SPS mit dem Siemens TIA Portal, wobei man zwischen folgenden Programmiersprachen wählen kann:
- Anweisungsliste AWL
- Kontaktplan KOP
- Funktionsplan FUP
- Structured Control Language SCL
- S7-Graph AS
Die Lernenden erstellen mit Hilfe von YoutTube Videos ein SPS Programm inklusive Visualiserung auf einem Touch-Panel. Das Progamm setzt Behältern einen Deckel auf, ähnlich wie es Pamasol bei den Aerosol-Anlagen macht. Dort werden Spraydosen mit einem Ventil, Sprühkopf und einer Kappe bestückt.
Unterabschnitte von Automatisierungsprojekt
Aufgabenstellung
Beschreibung des Programmablaufes
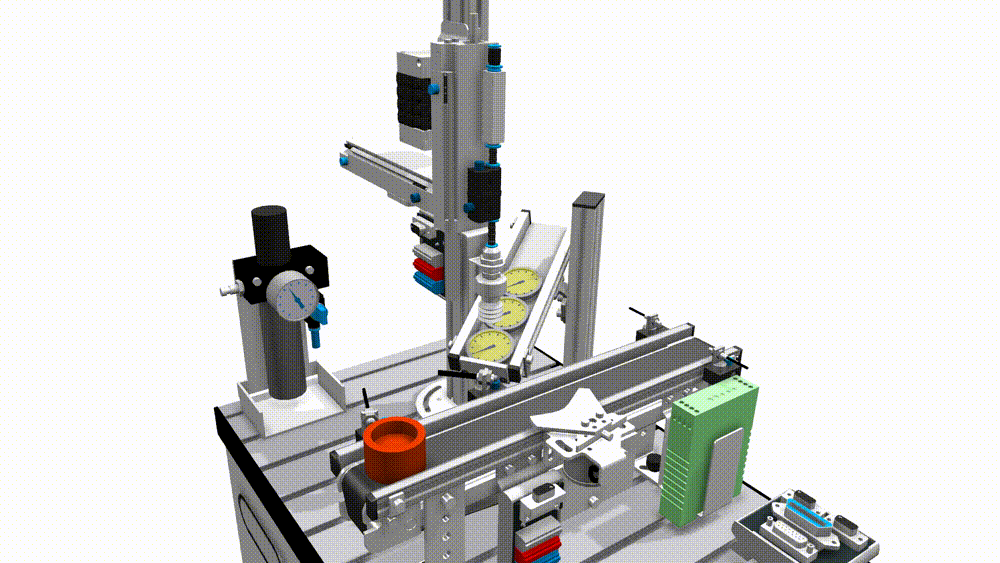
Wie in der Animation oben gezeigt, soll der Pick&Placer folgendermassen programmiert werden, inklusive Visualisierung am Bedienpanel.
- Zu Beginn ist der Pick&Placer eingefahren und das Förderband steht.
- Der Operator platziert einen Behälter auf dem Förderband bei der Einlauflichtschranke 100BG1 und drückt den Taster Start.
- Der Behälter wird bis zum Vereinzeler gefördert und dort gestoppt.
- Der Pick&Placer fährt nach unten, saugt beim Deckelmagazin einen Deckel an, fährt wieder nach oben, nach vorne und nach unten über den Behälter.
- Vakuum wird gelöst und somit Deckel aufgesetzt.
- Der Pick&Placer fährt wieder in die Startposition.
- Der Vereinzeler lässt den Behälter mit aufgesetztem Deckel weiterfahren.
- Kommt der Behälter an der Rückstau Lichtschranke 100BG3 an, stoppt das Förderband.
Die Positionen der wichtigsten Sensoren können folgender Grafik entnommen werden.
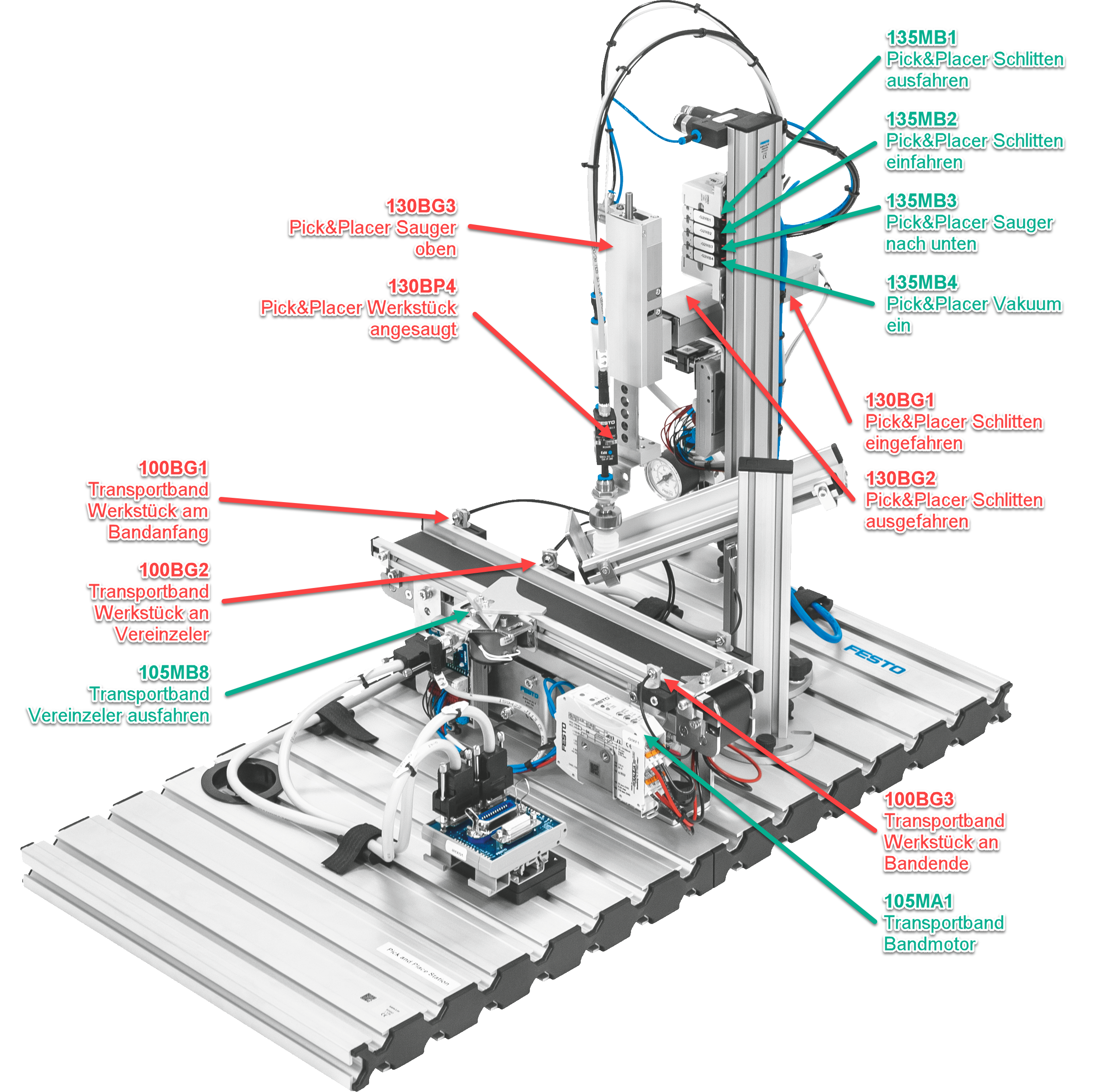
Info
Das Elektroschema des Steuerschranks kann hier als PDF heruntergeladen werden
Dokumentation
Die mit Kommentaren versehenen Projekte können als TIA Archivdatei (*.zap16
, *.zap17
usw.) aus folgender Tabelle heruntergeladen werden.
Name | Lehrjahr | Lehrberuf | Programm |
---|
Stefan Feier | 2019-2023 | Automatiker | |
Nicolas Diethelm | 2020-2024 | Automatiker | Download ZAP16 |
Flavio Knobel | 2020-2024 | Automatiker | Download ZAP16 |
Kevin Kälin | 2021-2025 | Automatiker | |
Linus Lacher | 2022-2026 | Automatiker | |
Kurzübersicht TIA V16
Wie die Entwicklungsumgebung TIA Portal aufgebaut ist
Um eine SPS programmieren zu können, benötigt man einen Laptop, auf welchem die SPS-Programmiersoftware – im Fachjargon Entwicklungsumgebung genannt – installiert ist.
Der Pick&Place Roboter ist mit einer Siemens SPS ausgestattet, welche mittels der Entwicklungsumgebung TIA Portal programmiert wird. TIA ist die Kurzversion für «Totally Integrated Automation». Mehr Infos zu dieser Software gibt es auf der Siemens Webseite.
Im Video wird die Benutzeroberfläche erklärt mit den beiden Ansichten Portalansicht und Projektansicht. Zudem wird gezeigt, wie die Online-Hilfe funktioniert.
Neues Projekt erstellen
Die SPS Hardwarekonfiguration als Basis
In einem ersten Schritt wird in der Projektansicht ein neues SPS Projekt erstellt. Anschliessend muss man die im Schaltschrank verbaute SPS in der Software abbilden. Das wird mittels Hardwarekonfiguration gemacht.
Der Pick&Place Roboter ist mit einer SIMATIC ET200 CPU ausgestattet. Zusätzlich werden die Ein- und Ausgangsmodule hinzugefügt und konfiguriert.
Artikelnummern der SPS für Hardwarekonfig
- Steuerung CPU 1512SP F-1 PN:
6ES7512-1SK01-0AB0
- Safety Eingangskarte ET200SP F-DI 8x 24V DC HF:
6ES7136-6BA00-0CA0
- Safety Ausgangskarte ET200SP F-DQ 8x 24V DC/0.5A PP
6ES7136-6DC00-0CA0
- Digitale Eingangskarte ET200SP DI 16x 24V DC ST:
6ES7131-6BH01-0BA0
- Digitale Ausgangskarte ET200SP DQ 16x 24V DC/0.5A ST:
6ES7132-6BH01-0BA0
- Analoge Eingangskarte ET200SP AI 2x U/I 2/4-Wire HS:
6ES7134-6HB00-0DA1
- Analoge Ausgangskarte ET 200SP, AQ 2xU ST:
6ES7135-6FB00-0BA1
Modulkarten parametrieren
Central processing unit (CPU) und IOs konfigurieren
In der Gerätekonfiguration werden die Module so benannt, dass sie dieselben Namen wie im Elektroschema haben. Anschliessend wird der Adressbereich vergeben über das Eigenschaftsfenster. Alternativ kann man die Ansicht Gerätesicht > Geräteübersicht anwählen. Dort sind alle Karten und die Adressbereiche in Tabellenform gelistet.
Die BaseUnits der Eingangs- und Ausgangsmodule gibt es in Hell- und Dunkelgrau. Hellgraue Module werden mit 24VDC gespiesen. Dunkelgraue Module werden nicht gespiesen, sie greifen die Spannung von Links ab. Im Projekt werden folgende BaseUnits verwendet:
Bei der absoluten Adressierung wird direkt der Operand (z.B. I0.0
) eingegeben. Bei der symbolischen Adressierung wird nicht der Operand, sondern stellvertretend ein Symbolname (z.B. CC_TB_24VMainOk
) anstelle des Operanden eingegeben.
- CC steht für Control Cabinet oder in Deutsch Schaltschrank. Es handelt sich somit um den Ort, wo das Bauteil eingebaut wird (Ortsaspekt des Objekts).
- TB steht für das elektrische Bauteil (Haupt- und Unterklasse nach EN 81346). In diesem Fall der Hilfskontakt des Netzgerätes
10TB1
. - 24VMainOk steht für die Kurzbeschreibung der Funktion in Upper Camel Case. In diesem Fall “24VDC Versorgung OK”.
Die Variabeln können in der Projektnavigation unter Geräte > PLC-Variabeln eingegeben und editiert werden. Im Video wird zusätlich auf die Excel Import und Export Funktion eingegangen.
Tipp
Das Excel File, welches als Import für die PLC Tags verwendet werden kann, findest du hier als Download
HMI parametrieren
4-Zoll Touch-Panel Siemens KTP400 Comfort
HMI steht für Human-Machine Interface oder in Deutsch für Mensch-Maschine-Schnittstelle. Es ist das Touch-Panel, mit dessen Hilfe der Operator die Maschine bedient.
Unter Geräte > Geräte und Netze wird das HMI hinzugefügt. Es handelt sich um ein KTP400 Comfort Panel von Siemens mit der Typennummer 6AV2124-2DC01-0AX0
.
Profinet steht für Process Field Network. Es ist ein Kommunikationsprotokoll, welches in der Industrie oft zum Einsatz kommt und TCP/IP Standards verwendet. Die Kommunikation zwischen SPS und HMI funktioniert somit ähnlich, wie das Internet (IP steht für Internet Protocol). Jeder Teilnehmer kriegt eine eindeutige IP-Adresse – die Profinet-Adresse. Jede Adresse darf im Projekt nur einmal vorkommen.
- Profinet-Adresse von HMI 155PH1:
192.168.10.5
- Profinet-Adresse von SPS 20KF3:
192.168.10.10
SPS simulieren
CPU und HMI emulieren für Tests ohne Hardware
Mit Hilfe von SIMATIC S7-PLCSIM kann die Pick&Place Steuerung simuliert und somit getestet werden, ohne dass irgendwelche Hardwarekomponenten benötigt werden.
Im Video wird die PLC und das Touch-Panel emuliert. Emulieren bedeutet die Funkionen eines Computers auf einem anderen Gerät nachbilden.
Um eine SPS oder ein HMI zu simulieren, muss man das Bauteil im Projektnavigator unter Geräte anwählen und anschliessend in der Symbolleiste auf das Icon Simulation starten klicken.
Anschliessend werden die gewünschten Bausteine geladen. Diese können fast im selben Umfang wie bei einer hardwaremässig angeschlossenen SPS getestet werden. Beispielsweise mit Beobachten ein/aus Funktion oder mit einer SIM-Tabelle.
Hier nicht entscheidend, aber für andere Projekte: Es können keine geschützten Bausteine in die Simulation geladen werden. Falls es diese im Projekt gibt, müssen sie zuerst freigegeben werden.
Programm laden
Download des Programms vom PC auf SPS und HMI
Um das Programm aus dem TIA Portal auf die SPS zu laden. In einem ersten Schritt klickt man unter Geräte auf Geräte & Netze, wo man sich die IP-Adressen einblenden lassen kann.
- CPU 1512SP F-1 PN:
192.168.10.10
- Touch-Panel KTP400 Comfort:
192.168.10.5
In einem zweiten Schritt muss man dem Laptop, welcher sich im gleichen Netzwerk befindet, eine statische IP-Adresse vergeben. In Windows bei den Adapteroptionen wählt man für den Ethernet-Port die Adresse 192.168.10.99
.
In der Symbolleiste wählt man das Symbol Laden in Gerät, um das Programm auf die SPS zu laden.
Da eine Safety Integrated SPS zum Einsatz kommt, müssen die beiden Safety Karten 20KF5
(Eingänge) und 20KF6
(Ausgänge) identifiziert werden. Man muss eine Profisafe-Adresse zuweisen.
Auf dem HMI klickt man auf Settings > Transfer > PN/IE > Properties… > PN_X1 > Specify an IP Address > 192.168.10.5
um die IP-Adresse einzustellen. Ebenfalls muss man im Anschluss auf Laden in Gerät klicken.
Programm erstellen
Erstes Programm für Pick&Place Roboter
Im Main [OB1] wird ein Programm erstellt, um die horizontale Achse des Roboters aus- und einzufahren. Dazu wird die grafische Programmiersprache KOP (Kontaktplan) verwendet mit folgenden Ein- und Ausgängen.
Beschreibung | Symbolische Adresse | Absolute Adresse |
---|
Pick&Placer Bedienstelle Start (160SF3) | PIPL_Pa_SF_Start | E1.1 |
Pick&Placer Schlitten ausfahren (125MB1) | PIPL_MB_CarrierExtend | A0.4 |
Pick&Placer Schlitten einfahren (125MB2) | PIPL_MB_CarrierRetract | A0.5 |
Pick&Placer Bedienstelle Stop (160SF4) | PIPL_Pa_SF_Stop | E1.2 |
PLC Clock 0.4s (2.5Hz) | ME_PLC_Clock_0.4s | M0.2 |
Pick&Placer Bedienstelle LED Start (160SF3) | PIPL_Pa_PF_Start | A1.2 |
Pick&Placer Turmleuchte Grün (130PF1) | PIPL_SC_Green | A0.1 |
Visualisierung erstellen
Bindeglied zwischen Mensch und Maschine entwerfen
Als HMI (Human Machine Interface) 155PH1 kommt ein KTP400 Comfort Panel von Siemens zum Einsatz. 400 steht für die Bidschirmgrösse, was in diesem Fall 4.3" ist. Die Auflösung beträgt 480 auf 272 Pixels.
Zum Vergleich: ein Samsung Galaxy S22 Smartphone mit einem 6.1" Display hat eine Auflösung von 1080 x 2340 Pixels. Bezüglich Design ist man somit etwas eingeschränkt, dennoch kann ein schönes und übersichtliches Design erstellt werden, welches dem Operator die Bedienung des Pick&Place Rotobers erleichtert.
In der Projektnavigation klickt man auf das HMI 155PH1. Unter Bildverwaltung > Vorlagen wird eine Vorlage erstellt. Im Laufe des Tutorials werden basierend auf der Vorlage folgende drei Bilder erstellt:
Bild_1 - Uebersicht
Bild_2 - Meldungen
Bild_3 - Schalter Etc
Mittels Schaltflächen können die Bilder und somit die Anzeigen gewechselt werden (Klicken > Ereignis). Der Datenaustausch zwischen PLC und HMI wird mittels Datenbaustein DB122
realisiert.
Neben einer Meldelampe mit Textliste wird eine Meldelampe mit Grafikliste erstellt.
HMI Alarmmeldungen
HMI-Bitmeldungen auf Touch-Panel anzeigen
Eine Störung, welche die rote Lampe aufleuchten lässt, ist bereiets vorhanden im Main [OB1], jedoch gibt es zu dieser Leuchte keine Fehlermeldung. Die Leuchte waltet als Sammelfehler. Sie wird in Netzwerk 7 generiert, wo es folgende Variabeln gibt.
Beschreibung | Symbolische Adresse | Absolute Addresse |
---|
Pick&Placer Schlitten ausgefahren (120BG2) | PIPL_BG_CarrierExtended | E0.5 |
Pick&Placer Schlitten eingefahren (120BG1) | PIPL_MB_CarrierRetracted | E0.4 |
Pick&Placer Schlitten ausfahren (125MB1) | PIPL_MB_CarrierExtend | A0.4 |
Pick&Placer Schlitten einfahren (125MB2) | PIPL_MB_CarrierRetract | A0.5 |
Störung aktiv | StoerungAktiv | M100.0 |
Um dem Operator spezifische Informationen zum Problem bereitstellen zu können, gibt es bei Siemens die Funktion HMI-Meldungen. Sie übernimmt das Handling der Meldungen und deren Anzeige auf dem Touch-Panel.
Damit man dem HMI Fehlermeldungen übergeben kann, muss man einen Datenbaustein DB erstellen mit Name HMI_Meldungen
, Typ Global-DB
und Nummer 120
. In einem zweiten Schritt erstellt man die Datenstruktur, welche aus 3 Struct von je einem Wort (1 Wort = 16 Bit) besteht, wovon je ein Struct für Fehler, Warnungen und Meldungen reserviert ist.
- Static
- Fehler (Struct)
Hzyl_nicht_ausfefahren
(Bool)Hzyl_nicht_einfefahren
(Bool)
- Warnungen (Struct)
- Meldungen (Struct)
In einem weiteren Schritt klickt man in der Projektnavigation unter 155PH1 das Menü HMI-Meldungen. Bei den Tabs wählt man Bitmeldungen und fügt folgende Bitmeldungen ein. Damit verknüpft man die Meldungen auf dem HMI mit dem Programm.
ID | Meldetext | Meldeklasse | Triggervariable | Triggerbit | Triggeradresse |
---|
1 | Horizontalzylinder ist nicht ausgefahren | Errors | Fehler | 8 | %DB120.DBX0.0 |
2 | Horizontalzylinder ist nicht eingefahren | Errors | Fehler | 9 | %DB120.DBX0.1 |
Im letzten Schritt wird ein Bild erstellt mit einer Meldeanzeige.
Programm strukturieren
OB1 in verschiedene Teilprogramme zerlegen
Der OB1
, in welchem sich das Programm befindet, wird in folgende drei FB's
aufgeteilt:
FB1
01-AllgemeinFB2
02-Allgemein_Pick&PlacerFB3
03-Ablauf_Pick&Placer
So kann man das Programm in kleine Teilaufgaben zerstückeln, was das Programm übersichtlicher macht. Zudem kann man wiederkehrende Funktionen wie das Bewegen einer Achse einmal programmieren und dann immer wieder verwenden – was dem DRY-Prinzip entspricht.
Bausteintyp | Kurzform | Merkmale |
---|
Organisationsbaustein | OB | - Schnittstelle zwischen Betriebssystem und Programm
- Gestaffelte Prioritäten (1 bis 28)
- zum Beispiel OB1, OB120
|
Funktionsbaustein | FB | - Parametrierbar (mit Gedächtnis)
- IN, OUT, INOUT, STAT, TEMP
- Verwendung von Instanz-Datenbaustein. Aktualparameter ersetzen Formalparameter.
|
Funktion | FC | - Liefert Rückgabewert an aufrufende Funktion
- Parametrierbar, aber nicht(!) speichernd
- zum Beispiel für mathematische Funktionen
|
Datenbaustein | DB | - Globale Datenspeicherung
- Lokale Datenspeicherung (Instanz-DB)
|
C-Sharp Projekt
Taschenrechner als portable *.exe Datei in C# programmieren
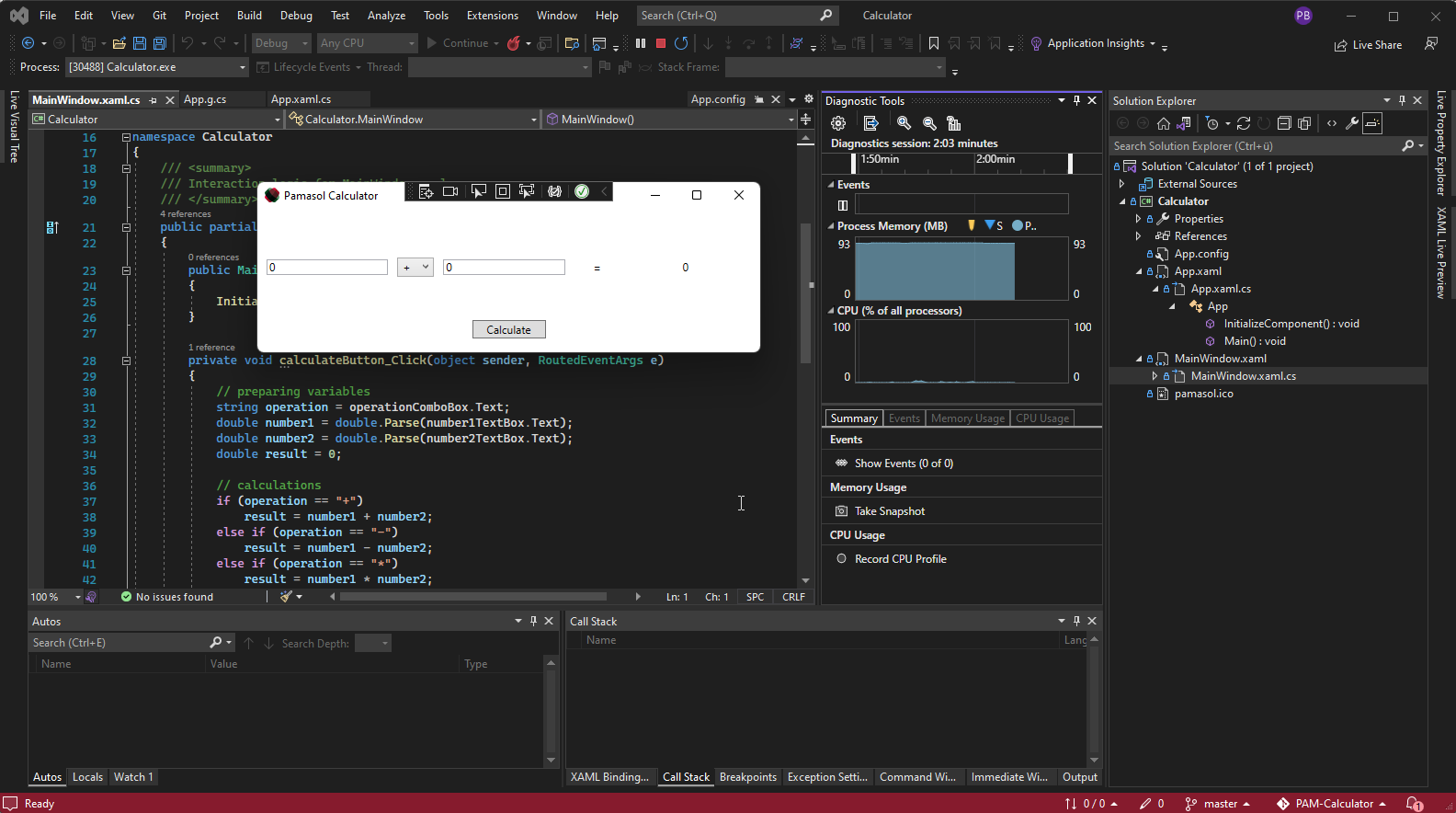
Neben Berufsschule, den überbetrieblichen Swissmechanic Kursen und dem praktischen Arbeiten an Aerosol-Anlagen für Kunden aus der ganzen Welt, arbeiten Automatiker Lernende bei Pamasol auch an Projekten, welche den Fokus auf ein bestimmtes Ausbildungsthema setzen.
PAM-Calculator repräsentiert das C#-Projekt der Ausbildung. Es soll Lernende in die objektorientierte Programmierung einführen.
Mithilfe der Visual Studio IDE (Integrated Development Environment) wird ein Windows Taschenrechner in C# programmiert. Der Rechner kann zwei Zahlen addieren, subtrahieren, multiplizieren und dividieren. Bei Division durch 0 wird eine Warnung ausgegeben:
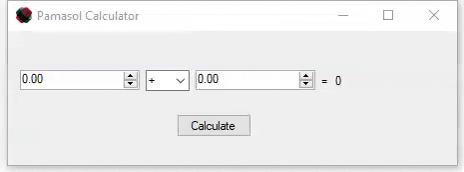
Die Exe-Datei, welche erstellt wird, kann auf einem PC mit Windows Betriebssystem ausgeführt werden.
Es wird eine Variante in Winforms und eine Variante in WPF erstellt, wobei beide Varianten im Anschluss verglichen werden.
Support
Kundensupport erhalten
Die Maschine läuft nicht, rote LEDs leuchten überall (oder nirgends), Linien-Bediener und Vorgesetzte schauen Sie mit der Erwartung an, das Problem im Nu zu finden und zu beheben.
In diesem Moment ist es wichtig, Ruhe zu bewahren, die Situation zu analysieren und allenfalls den Produkt-Support oder die After-Sales Abteilung vom Maschinenhersteller zu kontaktieren.
Dieses Kapitel beschreibt, wie man sich vorbereiten kann, um effiziente und schnelle Hilfe von der Pamasol After-Sales Abteilung zu erhalten.
Unterabschnitte von Support
Anfrage vorbereiten
In einem ersten Schritt muss das After-Sales Team die Seriennummer der betroffenen Maschine kennen. Im Falle eines Problems mit Elektrotechnik oder Software ist die Seriennummer des Schaltschranks entscheidend. Diese findet man auf dem Typenschild, welches auf der Türe ganz Link an der Innenseite angebracht ist. Siehe dazu folgendes Bild. Ein Beispiel für eine Seriennummer ist 12345-A1.
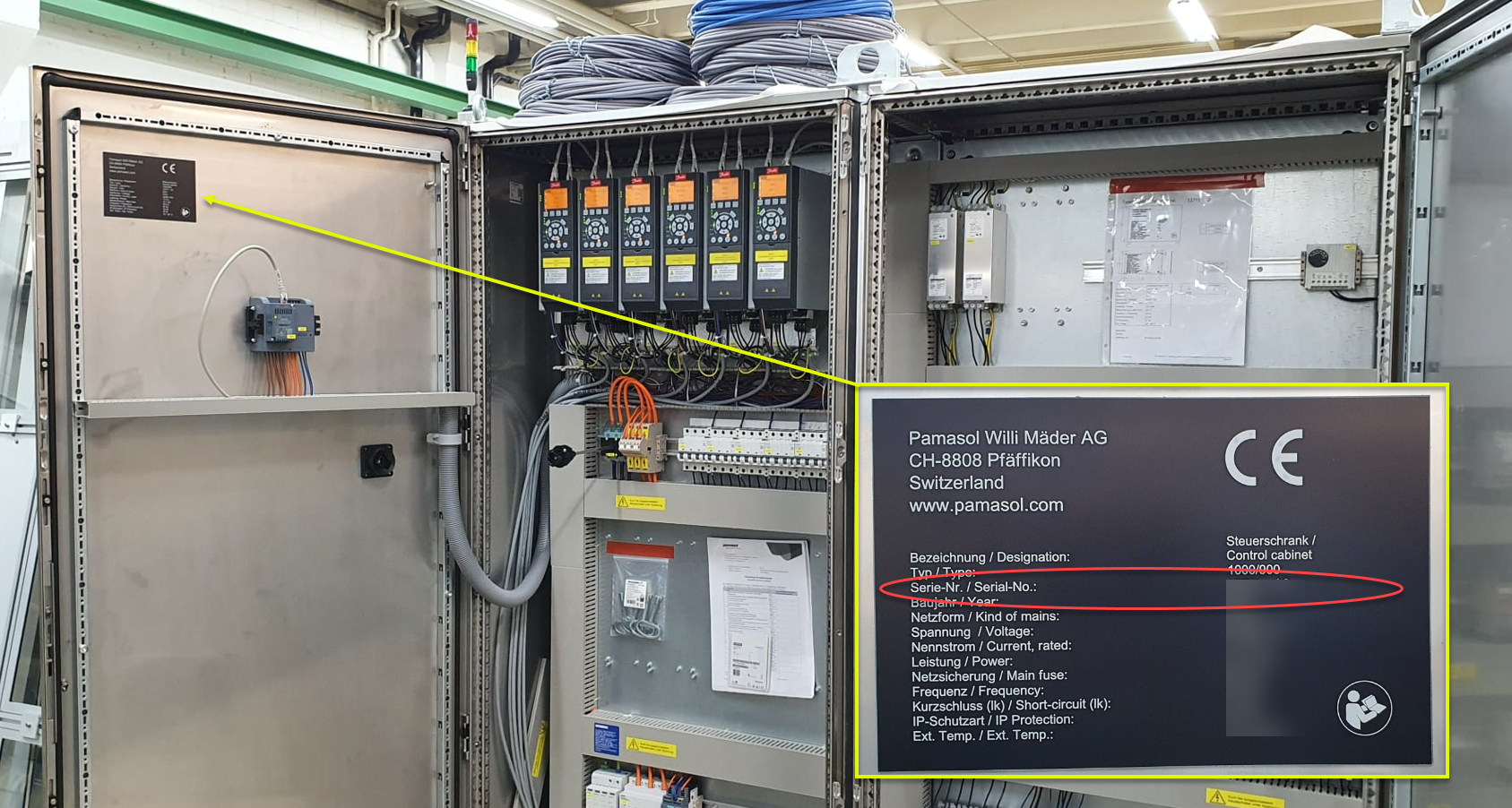
In einem zweiten Schritt muss der Fehler oder die Störung beschrieben werden. Im Idealfall hat man eine Antwort auf folgende Fragen:
Werden auf dem Touch-Panel Fehlermeldungen oder Warnungen angezeigt? Leuchtet an einer Bedienstelle oder einer Turmleuchte eine rote oder gelbe LED?
Wie unterscheidet sich das Verhalten der Anlage von der normalen Produktion? Läuft die Anlage gar nicht oder nur eingeschränkt?
Um welche Uhrzeit trat der Fehler auf? Ist der Fehler das erste Mal aufgetreten oder gab es das Problem schon früher?
Wurde vor dem Auftreten des Fehlers etwas geändert an der Anlage? Gab es beispielsweise einen Formatwechsel, Wartungsarbeiten, Schichtwechsel oder wurde das Rezept umgestellt?
War man zu einem früheren Zeitpunkt in Kontakt mit dem After-Sales Team bezüglich dieser Anlage?
Was wurde bereits unternommen zur Behebung der Störung? Respektive was wurde bereits getestet und geprüft?
Ist Pamasol in Bezug auf Hard- und Software auf dem neusten Stand? Wurden Änderung gemacht, ohne Pamasol zu involvieren? Beispielsweise eine Verdrahtungsänderung im Schaltschrank oder ein Wechsel eines Sensors oder Frequenzumformers?
Können Fotos und Videos zusammen mit der Fehlerbeschreibung bereitgestellt werden?
Fernwartung
Fehleranalyse und Support via Fernwartung
Die meisten Anlagen sind mit einem Fernwartungsmodul ausgestattet, welches eine sichere Verbindung via Internet von der Anlage zum Pamasol-Techniker herstellt.
Es handelt sich grösstenteils um ein blau gefärbtes Gerät von den Herstellern «EWON» oder «VIPA», welches im Hauptschaltschrank eingebaut ist. Das folgende Bild zeigt ein EWON Gateway.
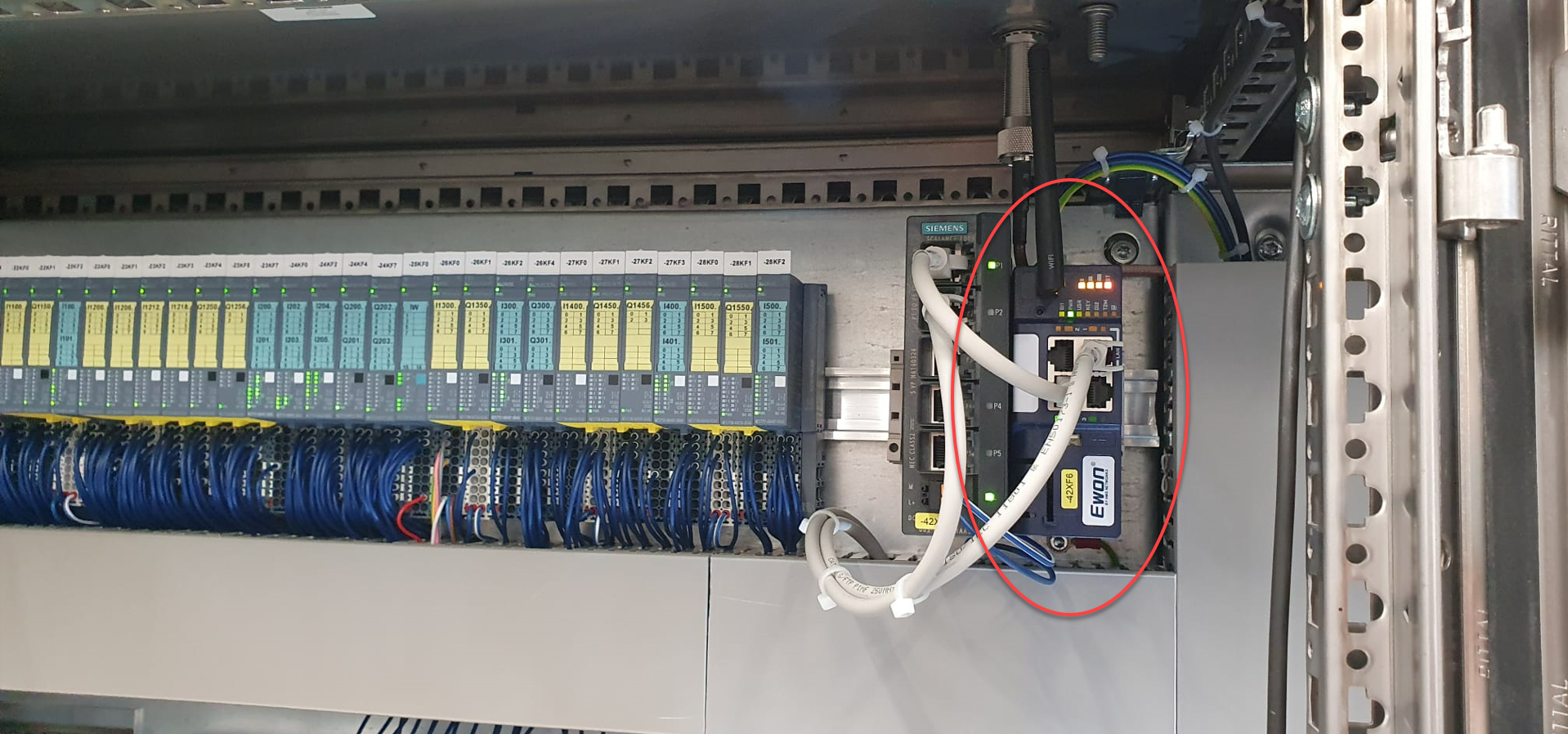
Suchen Sie nach dem Fernwartungsmodul im Schaltschrank und verbinden Sie das Ethernet Kabel, welches eine Internetverbindung bereitstellt, mit Port Nummer 4 (WAN Port), wie folgend gezeigt.
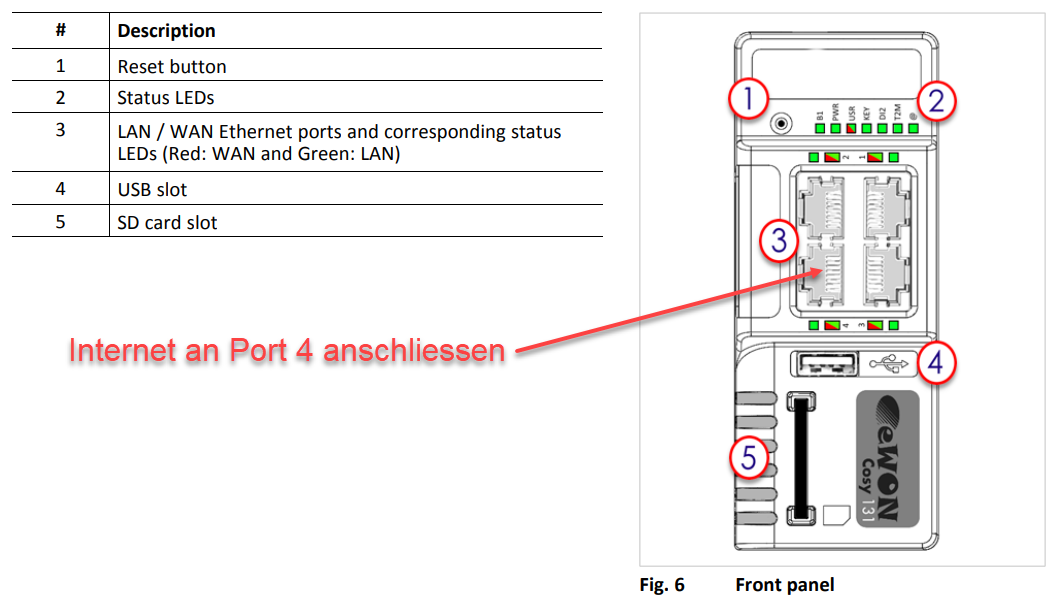
Bei einigen Modems ist zusätzlich ein Drehschalter eingebaut, mit welchem der Internetzugang des Modems hardwaremässig abgeschaltet werden kann. Prüfen Sie, ob dieser Schalter eingeschaltet ist.
Folgende Status LEDs müssen leuchten, damit das Modem korrekt arbeiten kann:
- PWR = Dauerhaft grün
- USR = Langsam blinkend grün
- T2M = Dauerhaft grün
- @ = Dauerhaft grün
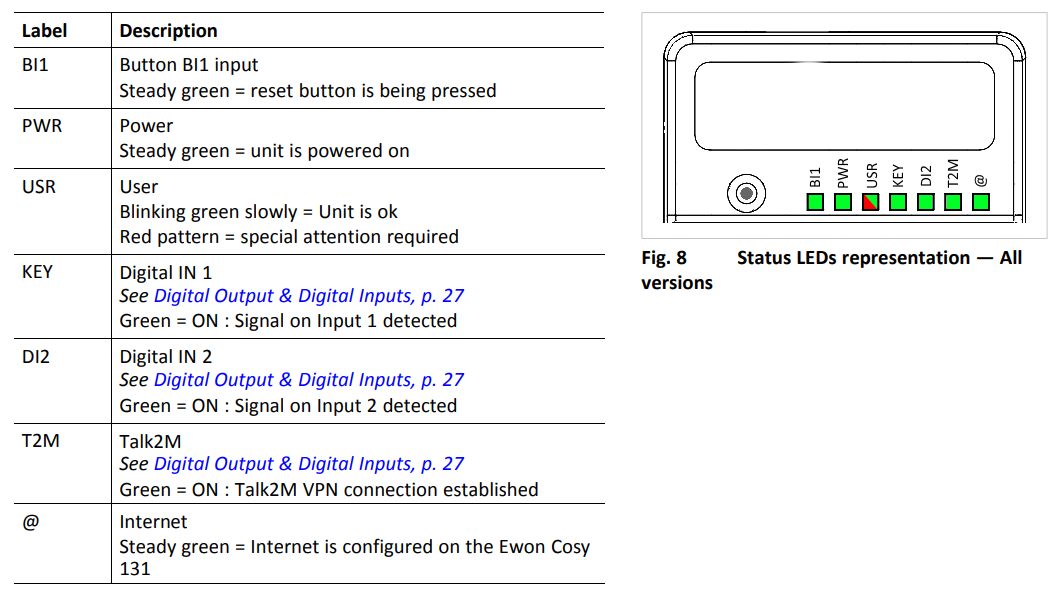
Das folgende Bild zeigt ein Modem, welches sich erfolgreich verbinden konnte. Zum einen leuchtet die @-LED, welche für Internetverbindung steht. Zum anderen leuchtet auch die T2M-LED, welche die erfolgreiche Anmeldung auf dem Fernwartungsserver anzeigt. Die orange LED beim RJ45 Stecker leuchtet permanent, während die grüne LED kurzzeitig unterbricht (Visualisierung Kommunikation).
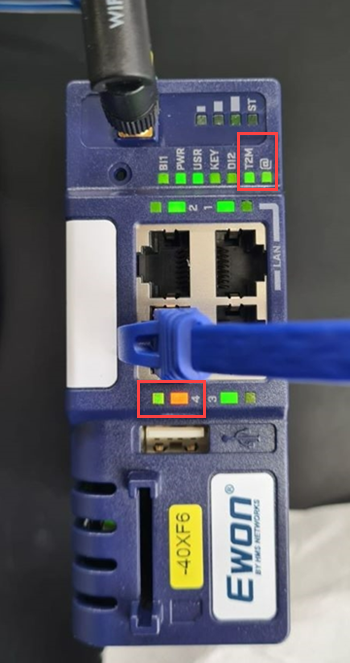
Firewall Einstellungen
Normalerweise muss Ihre IT-Abteilung nichts tun, damit sich das Modem mit dem Server verbinden kann. Der VPN-Tunnel wird vom Modem initiiert. Es gibt nur eine ausgehende Verbindung (HTTPS-Port 443 oder UDP-Port 1194) und keine eingehenden Verbindungen. Deshalb müssen in der Firewall keine Ports freigegeben werden.
Weitere Informationen zur Verbindung gibt es in diesem Dokument in Englisch.
Info
Wenn es Verbindungsprobleme gibt (und LED T2M nicht leuchtet), wird empfohlen, die URL *.talk2m.com
von Ihrer IT-Abteilung auf die Whitelist zu setzen.
Tipp
Wenn die IT-Abteilung keine Internetverbindung über das Firmennetzwerk zulässt, kann alternativ ein GSM-Modem verwendet werden. In diesem Fall sind Firmennetzwerk und Anlage strikt getrennt.